Eine kurze Betrachtung direkten Platinendrucks
Ich habe meinen für Platinen-Direktdruck modifizierten Lexmark E360d nun seit einer Weile im Einsatz. Details zum Bau selbst finden sich bereits im git-Repository des Projekts (englisch), daher beschränke ich mich hier auf einige Kommentare zur tatsächlichen Nützlichkeit. Platinenfertigung ist deutlich günstiger geworden, wodurch sich das Ätzen daheim kaum noch lohnt. Der „haxmark“ kommt bei mir daher nur noch zum Einsatz wenn ich eine Platine schnell brauche und dann leistet er anständige Arbeit.
Die grundsätzliche Idee
Ziel ist es, die Platine so direkt wie möglich vom Drucker ins Ätzbad geben zu können. Ich verwende normales kupferkaschiertes Platinenmaterial ohne Photobeschichtung, also wird der Toner Ätzresist sein. Um ihn auf die Platine zu bringen, muss der Laserdrucker umgebaut werden: Er sollte auf Platinenmaterial drucken wie auch auf Papier. Normaler Toner ist sehr beständig und hält später ohne Probleme den Chemikalien stand.
Da Platinenmaterial deutlich dicker und starrer als Papier ist, sind auf der mechanischen Seite einige Veränderungen nötig. Der Einzug wird seinen Dienst nicht tun bis weite Teile entfernt wurden. Anstatt wie das Papier über Rollen mehrfach umgeleitet zu werden, wird die Platine auf einem dünnen Träger vorne eingezogen und geradeaus nach hinten durch den Drucker geleitet, bis es ihn durch einen neue Öffnung auf der Rückseite verlässt. Optik und Photoleiter sind noch an ihrem Platz und lagern den Toner direkt auf der Kupferseite ab.
Nachdem ein großer Teil der Mechanik fehlt, fehlen auch die meisten Sensoren, von denen die Steuerung des Druckers im normalen Betrieb Signale bekommt, sowie das Papier sich fortbewegt. Im Falle unerwarteter Signale wird der Druckvorgang unterbrochen um Schäden am Drucker zu vermeiden. Soll der modifizierte Drucker also auch noch arbeiten und nicht nur Papierstaumeldungen produzieren, müssen diese Signale nachgestellt werden. Eine kleine Platine mit Mikrocontroller dient daher als Ersatz für entfernte Mechanik und Sensoren und schickt alles an die Druckerhauptplatine, was diese erwartet.
Der Druckvorgang muss außerdem ohne Fixiereinheit funktionieren. Dieser würde nicht genug Hitze abgeben und hätte ohnehin Probleme mit der Dicke des Mediums. Die Tonerpartikel halten daher nur durch elektrostatische Kräfte am Kupfer, wenn die Platine hinten ausgegeben wird. Diese sind zwar stärker als man denken würde (auch einem Pusten über die Oberfläche halten sie Stand), aber nicht stark genug fürs Ätzbad. Eine einfache Lösung ist es, die Platine in Acetondampf zu hängen, was die Druckqualität nicht beeinflusst aber den Toner leicht anlöst und den Druck dadurch sehr beständig macht.
Das ist, grob zusammengefasst, der ganze Druckprozess. Das Ätzen selbst funktioniert wie immer, aber der Vorgang davor ist nun deutlich vereinfacht.
Verwendung Schritt für Schritt
Ich erstelle meine Platinen in KiCad, das genaue CAD-Programm ist für den Druck aber nicht weiter relevant. So gehe ich typischerweise vor:
- Die Kupferlage wird als PostScript exportiert und mittels eines Skripts in die linke obere Ecke, mit empirisch ermitteltem Versatz, einer DIN-A4-Seite verschoben. Andernfalls würde es auf die Position des Layouts im CAD ankommen und doppelseitige Platinen wären wesentlich schwieriger auszurichten.
- Ich suche mir ein passendes Stück Platinenmaterial aus und biege es durch wiederholtes vor- und zurückbiegen gerade.
- Die Kupferoberfläche wird mir Schleifvlies abgerieben, bevor Kupferstaub und sonstige Rückstände mit ein wenig Aceton abgewischt werden. Scharfe Kanten, die den Photoleiter beschädigen könnten, runde ich ebenfalls ab.
- Das Platinenmaterial muss nun am Träger befestigt werden. Ich verwende dafür 5 mm breites Kupferklebeband (unkritisch, so lange die Platine gut hält und das Klebeband nicht im Weg ist). Ein elektrischer Kontakt zwischen Träger und Kupferoberfläche ist notwendig, allerdings zeigte sich normales Kupferklebeband, auch ohne leitfähigen Kleber, als mehr als ausreichend.
- Der Druck funktioniert PC-seitig wie üblich. Der Träger wird so weit eingeführt, dass die Rollen ihn erfassen können und mit einem Druck auf „OK“ startet der Druckvorgang. Sobald der Träger den Drucker wieder verlässt, prüfe ich die Platine auf offensichtliche Defekte.
- Die bedruckte Platine wandert in ein Gefäß mit ein wenig Aceton am Boden. Sie liegt dabei erhöht, sodass sie nur vom Dampf erreicht wird. Einige Minuten später ist der Toner ausreichend hart.
- Kleine Fehlstellen können mit wasserfestem Folienstift korrigiert werden.
Um doppelseitige Platinen ätzen zu können, wiederhole ich den gesamten Prozess, wobei eine Seite beim Ätzen jeweils mit breitem Klebeband abgedeckt wird. Es wäre theoretisch möglich, beide Seiten auf einmal zu ätzen, ich habe nur noch keinen Rahmen zum Halten im Acetondampf gebaut, damit die untere Seite nicht verwischt wird.
Vor- und Nachteile
Das Verfahren ist nicht perfekt. Einige Bemerkungen, falls jemand ans Umbauen eines Druckers für diese Aufgabe denkt:
Gut funktioniert:
- Die Auflösung ist ausgezeichnet. Strukturen bis 5 mil funktionieren ohne Probleme, die Toleranzen sind auch kein Thema.
- Der Toner ist sehr strapazierfähig, ich dachte bereits darüber nach, den Drucker für die Beschriftung metallener Frontplatten zu verwenden.
- Die Ausrichtung doppelseitiger Platinen ist nicht schwieriger als beim Belichten. Mein Träger bekam einen Streifen Metall als Anschlag, was das deutlich vereinfacht.
- Sobald die Platine aus dem Drucker kommt, sieht man wie das Endresultat nach dem Ätzen sein wird und kann auch noch kleine Probleme ausbessern. Es gibt keine Zwischenwerte wie beim UV-Belichten.
- Und, natürlich, es geht schnell.
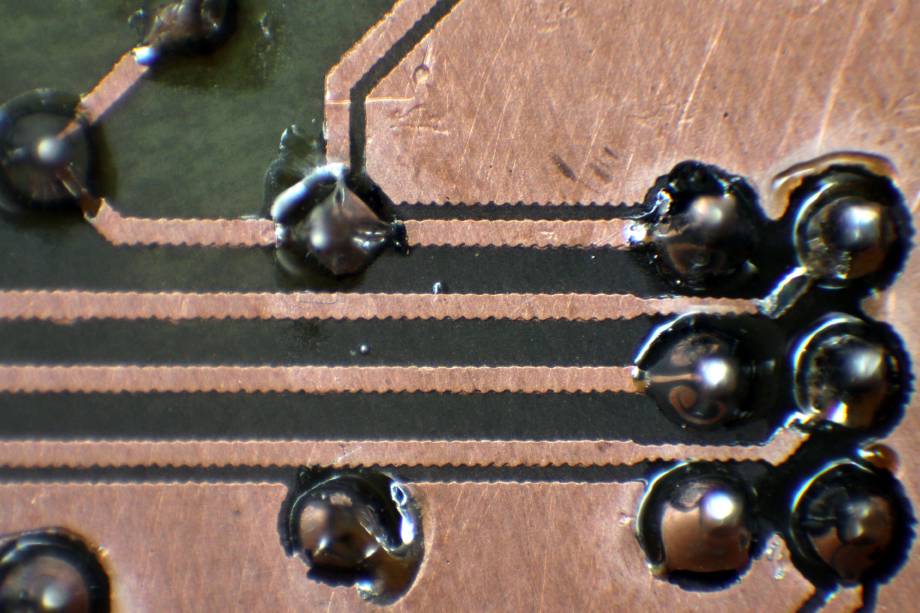
Luft nach oben:
- Der Photoleiter ist sehr empfindlich. Scharfe Kanten müssen stets entfernt werden, oder er ist schnell beschädigt.
- Ebenso zum Problem werden kann die Öffnung auf der Rückseite: Das Streulicht beschädigt den Photoleiter auf Dauer, falls sie nicht abgedeckt wird.
- Der Drucker reagiert wesentlich empfindlicher auf Unebenheiten des Platinenmaterials, als ich dachte. In der Tat ist das das größte Problem für mich: Kleine Ungleichmäßigkeiten führen schon zu Löchern im Druck und praktisch alles Platinenmaterial, was ich habe, ist deutlich verzogen. Mit der größte Teil verfällt daher darauf, das Platinenmaterial geradezubiegen.
- Eine leitfähige Oberfläche ist nötig. So etwas wie Bestückungsdruck für eine einseitige Platine ist damit leider nicht drin.
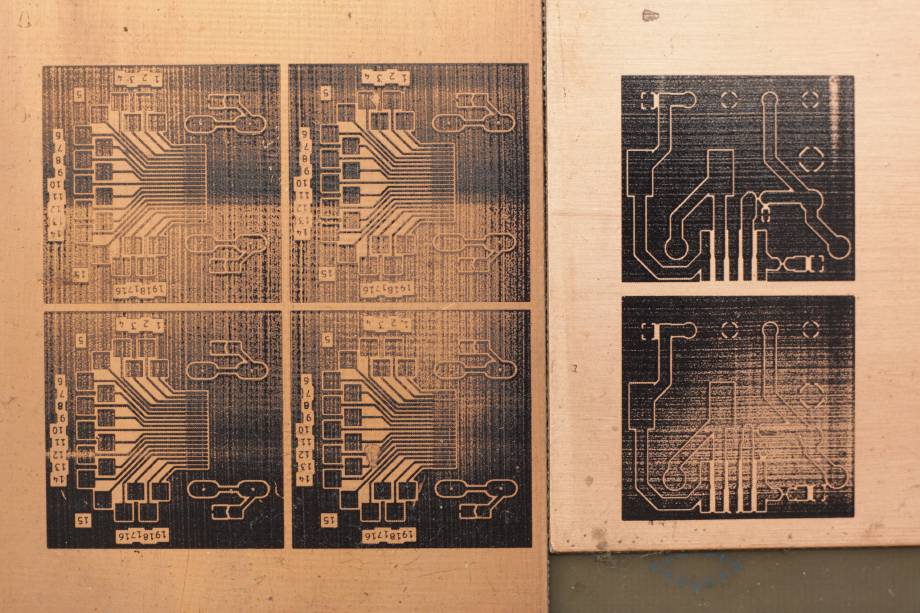
Bei meiner Verwendung übertreffen die Vor- die Nachteile immer noch. Ich habe zwar immer noch alles für die UV-Belichtung da, habe es aber nicht mehr gebraucht, seit ich den „haxmark“ gebaut haben.